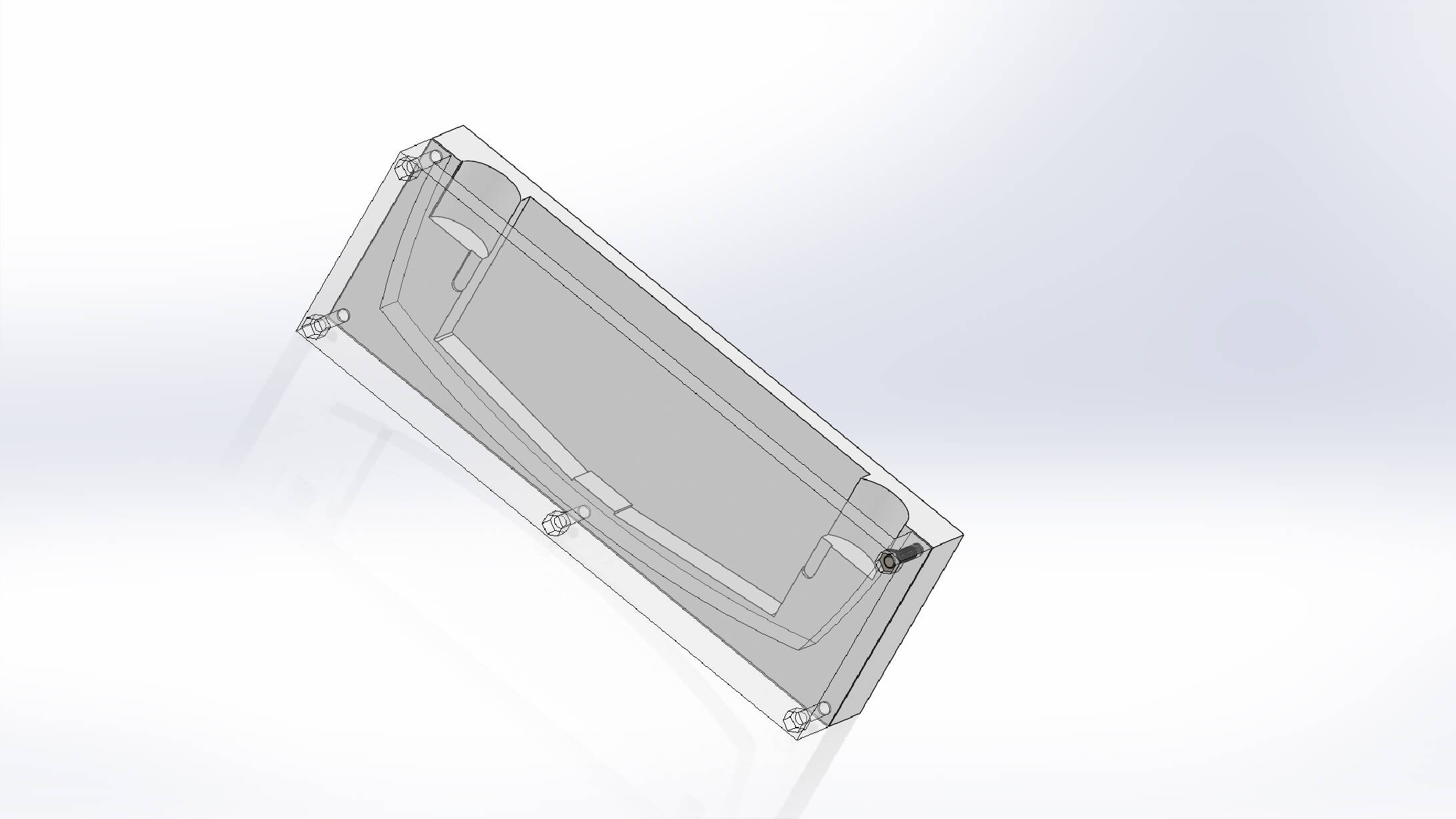
There was recently a post on this blog regarding our 3D printer used for making samples and prototypes. The 3D printer allows both our customers and us to enjoy speed and flexibility in various process steps. For instance, this is true for the start-up Steasy®: We printed a mount designed to hold the start-up’s custom battery pack during the vibration test, which is part of the UN 38.3 transport test.
From cell selection to certification with Jauch
Let us first take a general look at the various steps involved in battery projects. The process usually begins with defining the relevant parameters, including the required currents, battery life, space available, and external influences. We at Jauch have an exceptionally large cell portfolio at our disposal, meaning our customers are able to find the optimal cell swiftly. If required during consultation, we can also help them with the mechanical design, battery electronics, assembly, testing, certifications, and shipping.
Of course, this is not a rigid process that has to be followed exactly, as clearly illustrated by Steasy®.
Steasy®: a start-up from Switzerland
The people behind Steasy® are founders Claudio Ruiz, Johannes Hofer, and Reto Muhl. While they were still studying at university, the three of them came up with the idea of developing a battery-powered mini steamer that people can use to heat up their food on the go whenever they like. The method that they developed is so sophisticated that it doesn’t cause any loss of flavor or vitamins – compromises you otherwise have to accept when warming up food in a microwave.
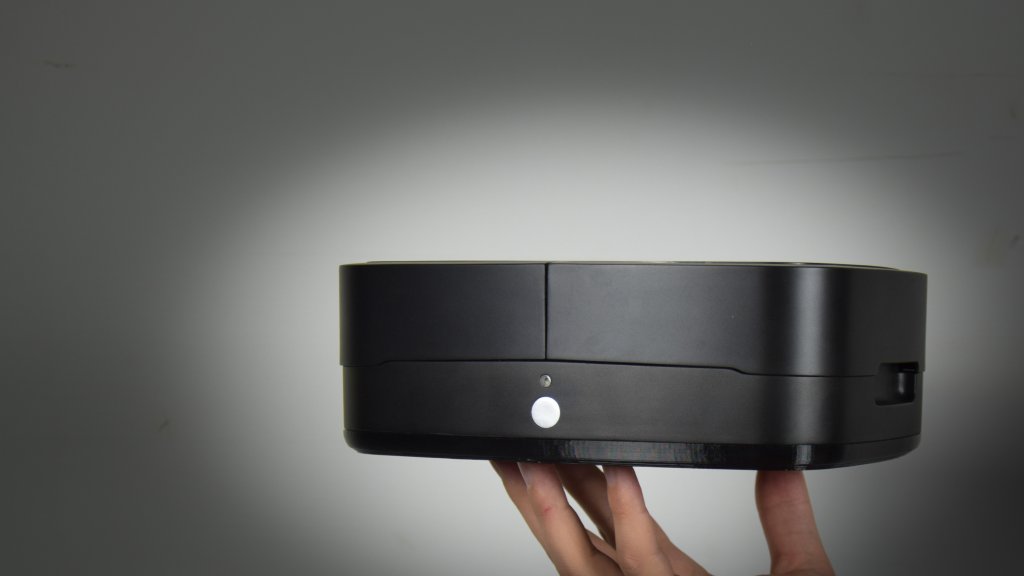
Steasy® meets Jauch
You’ve probably already identified the common thread between the start-up and Jauch: the battery. The start-up was initially only looking for a new cell supplier. After initial discussions, it was quickly clear that Jauch is able to not only supply cells to Steasy®, but also to support the company in this regard with a great deal of expertise.
“There was already an initial mechanical and electronic design of the pack at the beginning of our collaboration. Nevertheless, we recommended Steasy® to let our experts have another look at the design to ensure that the battery pack will pass the UN 38.3 transport tests,” explains Sales Manager Jérémie Deloof. No sooner said than done. After an analysis of the design’s electronic and mechanical aspects, the start-up received a few valuable tips on how to meet the requirements of the UN 38.3 transport tests.
Discussions were held with Project Manager Viktor Sichwardt about the selection of appropriate cells. Due in part to availability issues, another cell is now going to be used in the mini steamer. “At first, Steasy® planned to use 18650 lithium cells in the product. But now we have decided to go with cells of type 21700 – the advantage here is that these cells have a far higher capacity and are thus more suitable for the mini steamer,” says Mr. Sichwardt.
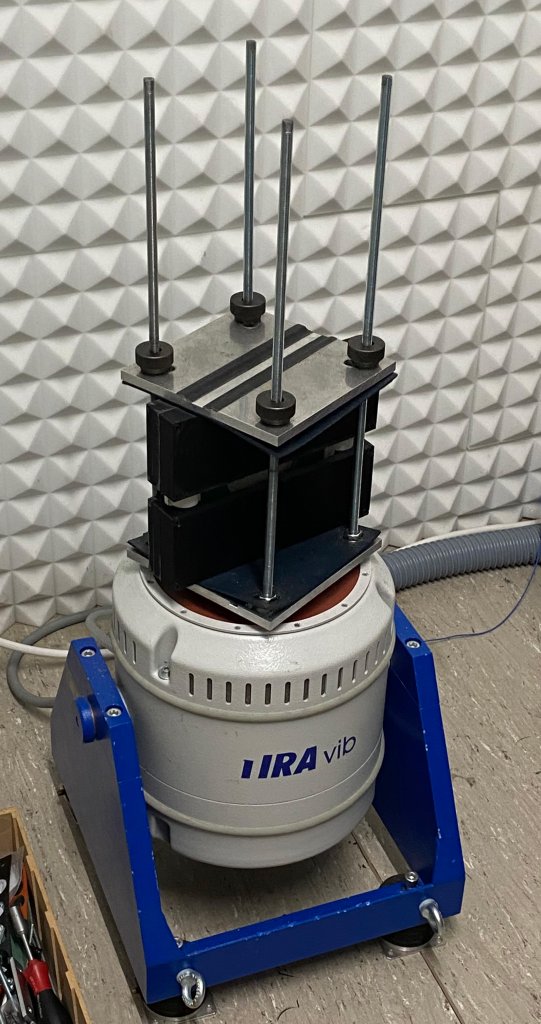
Likewise relevant to the start-up is the topic of battery certification, including the UN 38.3 transport tests – which are mandatory for batteries. Our in-house test center means that the tests can be performed at our location in Villingen-Schwenningen. The vibration test is one of the required tests. It involves shaking a battery pack in different axes for nine hours each at various frequencies. The objective is to evaluate whether all components on the battery pack (e.g., terminals) are properly fastened and make sure nothing comes loose. If parts of a battery pack break off and get thrown around, it could result in power interruptions or even complete failure.
Customized 3D-printed mount for the vibration test
A customized mount was needed for performing the vibration test – exactly the job for our 3D printer. A CAD model was necessary for the 3D print. And the model was created in Schwenningen as well. The design and printing process was wrapped up after just five days.
The mount consists of two parts that hold the test specimen (i.e., the battery pack) between them. Every battery pack comes with certain production tolerances. To compensate for these variations, a nut was embedded into one part of the 3D print. With the help of a screw on the other part, the mount is able to compensate for both positive and negative tolerances. This ensures that the specimen is held firmly in place throughout the test. Otherwise, the battery pack may develop its own dynamic, which could distort the result or cause unintentional damage.
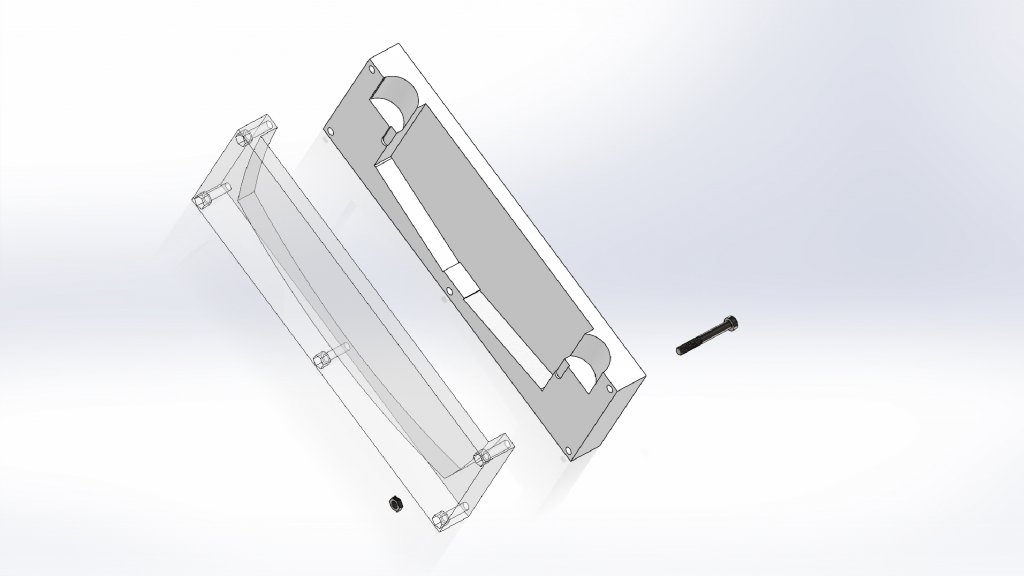
Our sample and prototype team subsequently used the 3D printer to make the two parts for the mount. “3D printing is particularly well suited to making such tools, as it lets us produce customized parts inexpensively, flexibly, and in a relatively short time,” says Patrick Nicosia, Battery Production Manager.
On site in Schwenningen for the vibration test
It was finally time: Reto Muhl and Claudio Ruiz came to Schwenningen and witnessed the vibration test in person. On the connected monitors, they were able to observe in real time whether or not the battery pack’s behavior fell within the standard during the test.
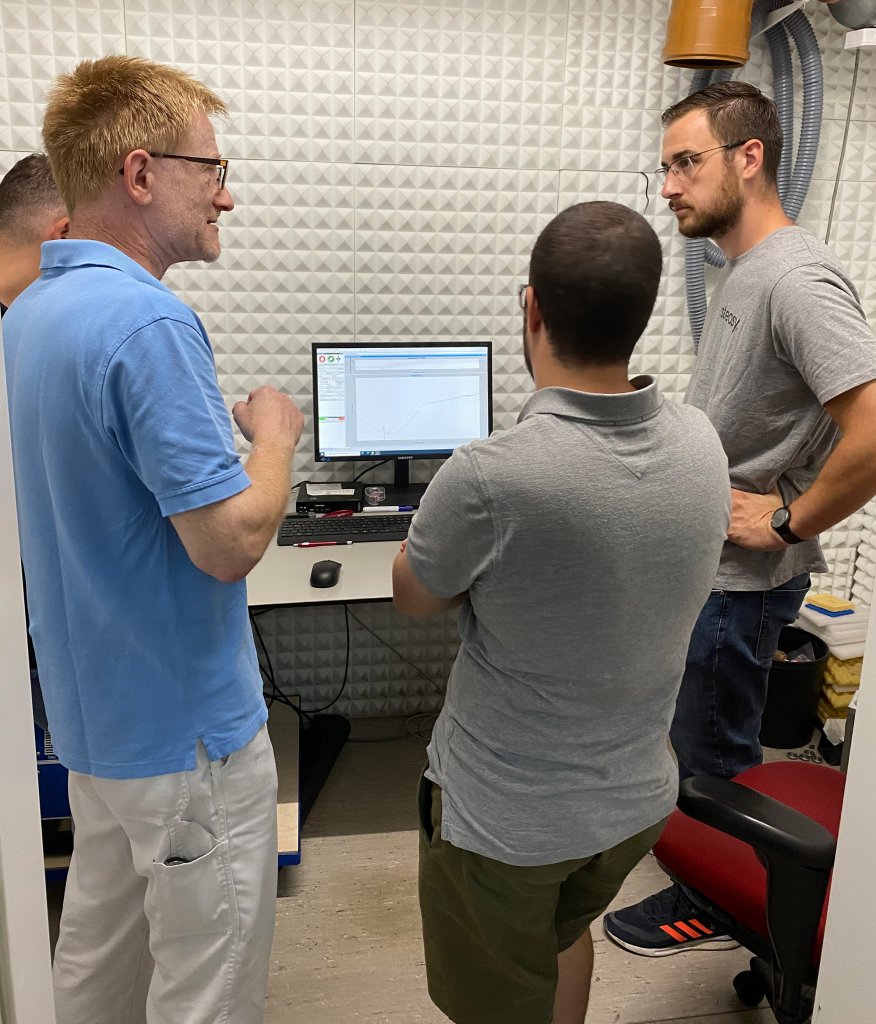
Right now, other tests are still being conducted to assess whether the battery pack fulfills all requirements. The founders are incredibly pleased: “Jauch has impressed us with a comprehensive package of services. The consultation has gone above and beyond our initial request for cells and is extremely valuable in view of the upcoming certifications. It was quickly apparent that we share the same understanding of quality,” explains Reto Muhl. According to Claudio Ruiz, regionality was another crucial factor in their decision to work with Jauch. “We are based in Switzerland, and it was important to us that we collaborate with people who are in the same time zone, speak the same language, and are approachable. Jauch’s location in Schwenningen makes it even better because this allows us to visit the facilities in person.”
Do you also need support in your battery project? More information about the process can be found here.
Your contact person:
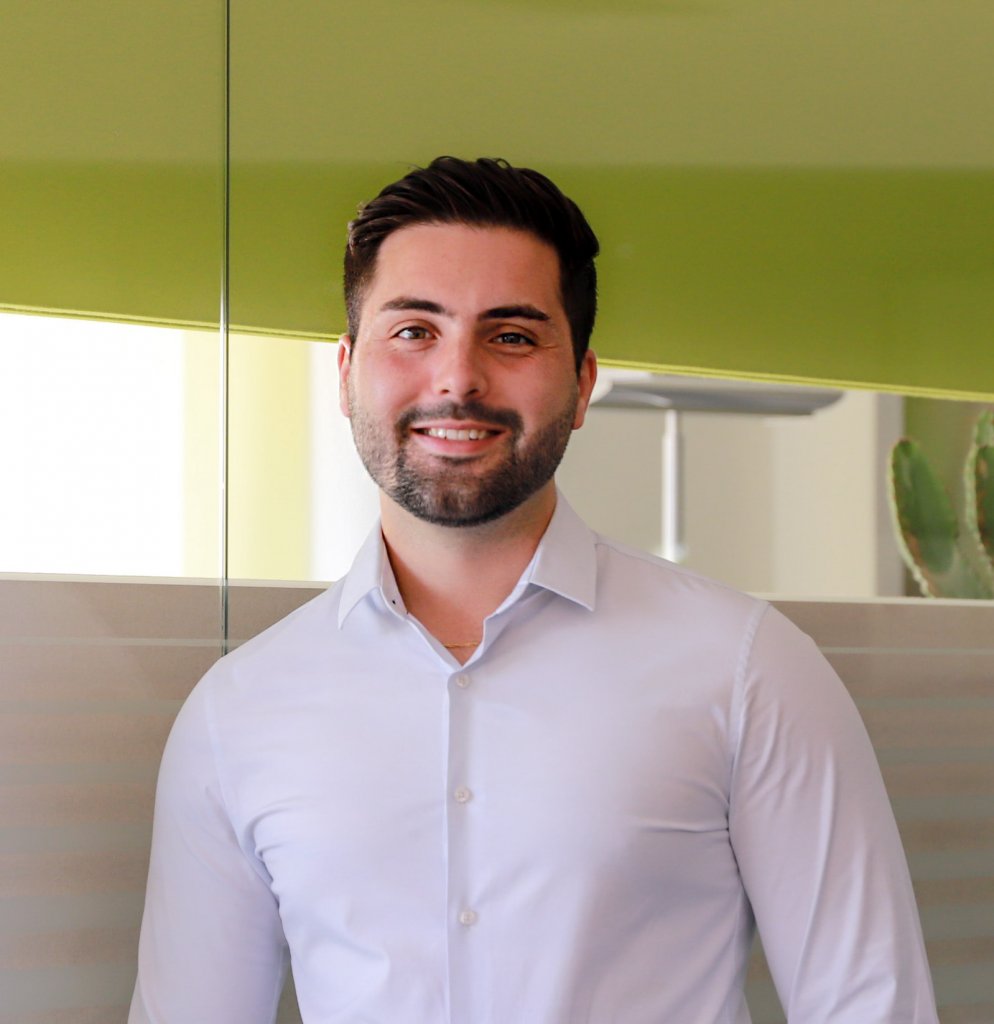
Jérémie Deloof, Sales Manager
+49 7720 945 177